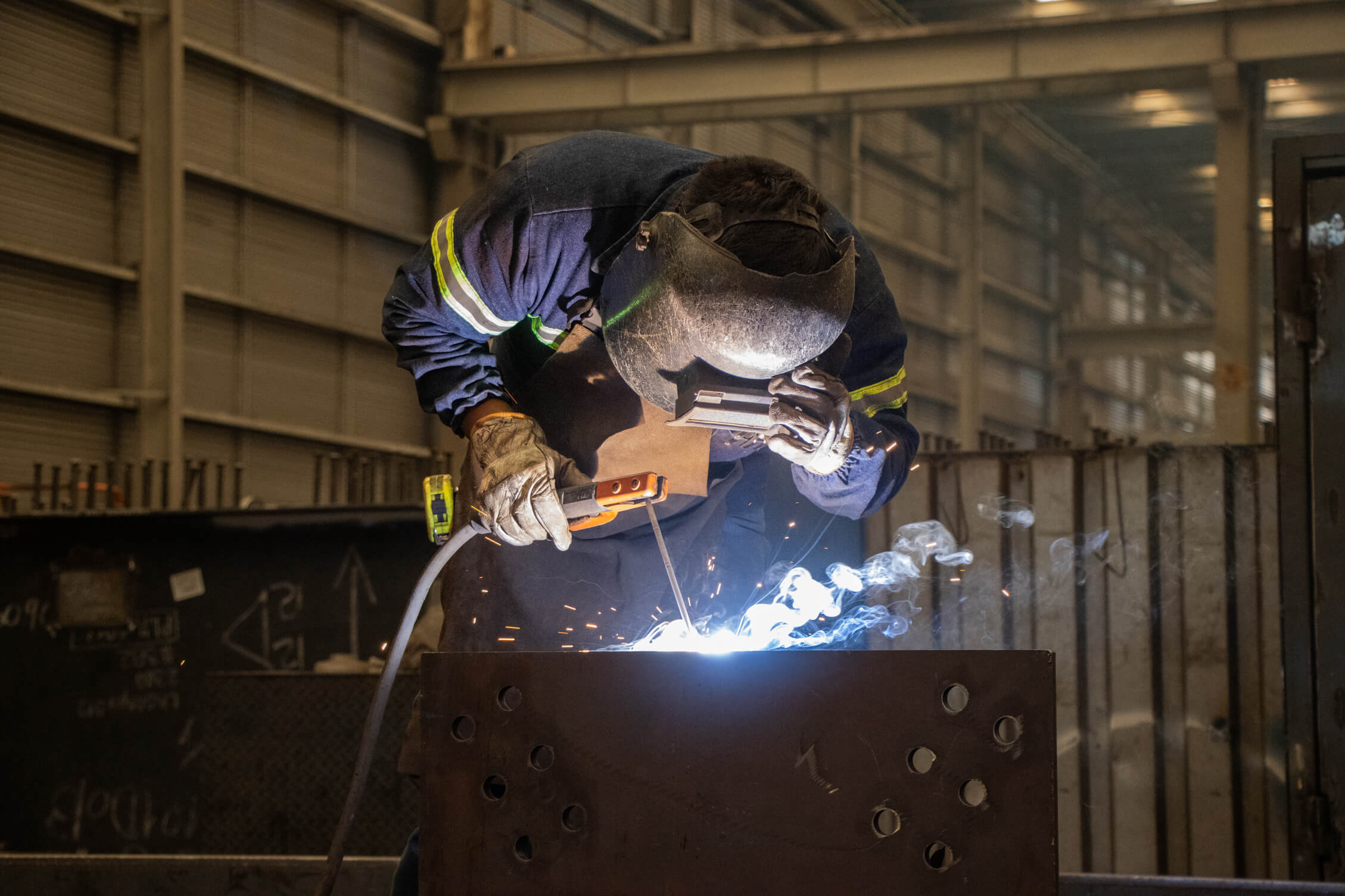
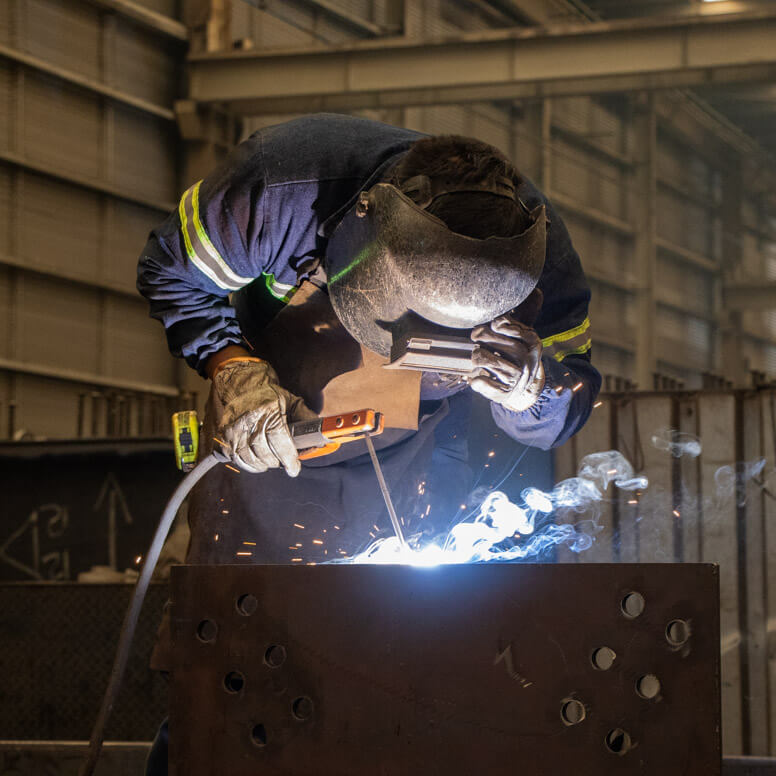
Qualified Welding Processes
In the steel structure manufacturing industry, quality and efficiency are key factors that determine project success. Welding is a fundamental process in creating these structures, and opting for qualified procedures can make a significant difference in terms of productivity, costs, and final quality. In this article, we’ll explore how FCAW-G, SAW, and ESW welding processes enhance competitiveness in steel structure manufacturing.
1.FCAW-G Welding (Flux-Cored Arc Welding – Gas Shielded)
FCAW-G welding is an arc process that uses a tubular electrode with a core of flux material and a shielding gas. This method is ideal for indoor work and offers several advantages:
- Versatility: FCAW-G can be employed in various positions and across different types of steel and thicknesses, making it suitable for complex structures.
- High Welding Speed: This process allows for a high metal deposition rate, reducing manufacturing time and increasing productivity.
- Lower Sensitivity to Contaminants: With the use of shielding gas, FCAW-G welding is less prone to oxidation and other contaminants, improving weld quality.
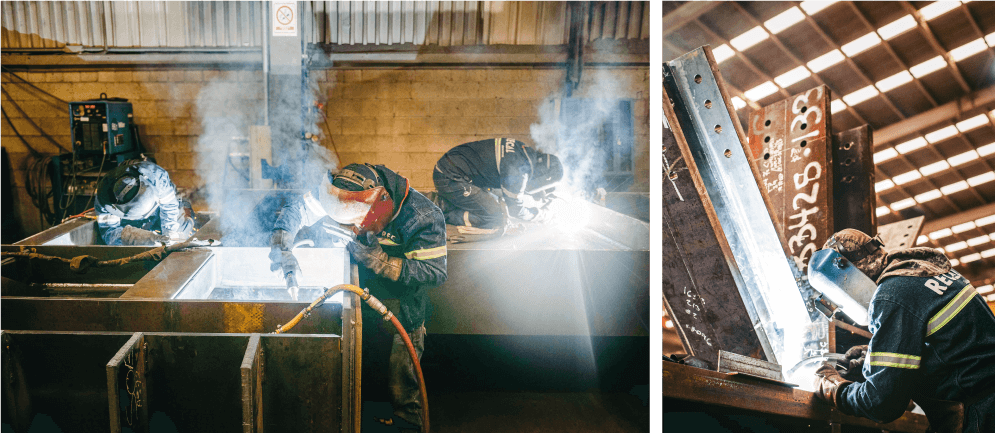
2.SAW Welding (Submerged Arc Welding)
SAW welding is a semi-automated process that uses an arc submerged in flux material. This method is especially beneficial for manufacturing large structures in terms of thickness and length:
- Superior Quality: SAW provides a more uniform weld bead with a high level of soundness, resulting in greater structural integrity and improved quality.
- Efficiency: Being a semi-automated process, SAW enables efficient mass production, essential for large-scale projects.
- Application in Penetration Joints with Long Configurations: The high quality of welds produced with SAW reduces the need for testing and inspections, saving time and costs.
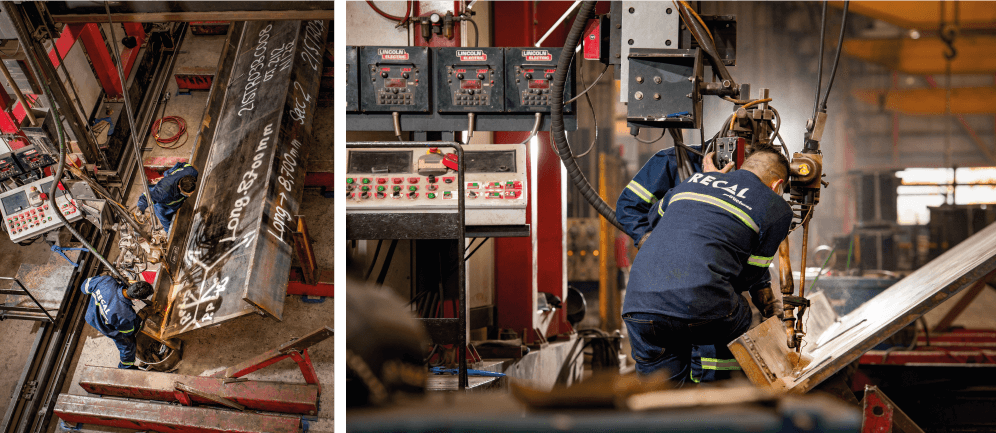
3.ESW Welding (Electroslag Welding)
ESW is another automated process primarily used for welding thick sections. Its advantages are noteworthy:
- High Productivity: ESW allows for high metal deposition per pass, leading to a significant reduction in welding time.
- Reduced Distortion: This process requires less preheating compared to other methods, minimizing distortion in the workpiece.
- Suitable for Large Thicknesses: ESW is ideal for steel structures with considerable thickness, making it perfect for industrial and commercial buildings with heavy-section profiles.
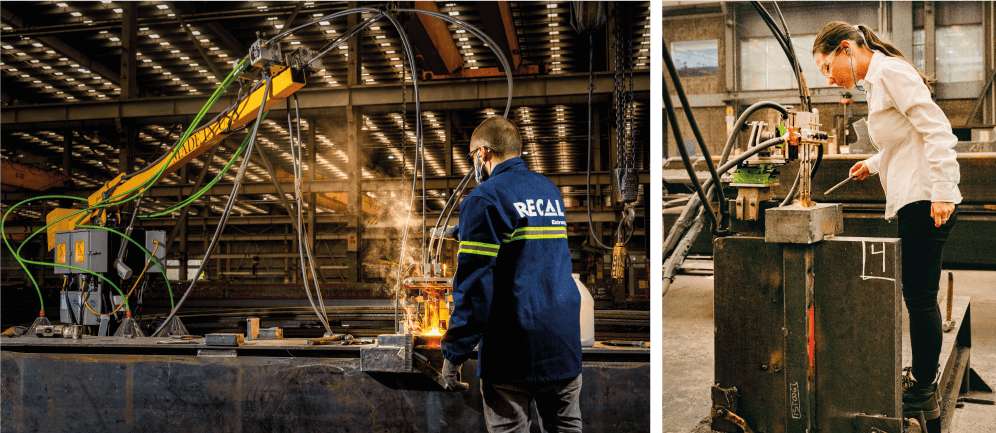
Conclusion
Choosing the right welding processes is crucial for optimizing steel structure manufacturing. FCAW-G, SAW, and ESW not only enhance work quality and efficiency but also provide a significant competitive advantage in an increasingly demanding market. Investing in qualified welding technologies can lead to cost reductions, shorter delivery times, and higher customer satisfaction, positioning the company as a leader in the steel structure construction industry.
By adopting these processes, companies can not only meet but exceed market expectations and customer requirements, ensuring long-term success in the industry